Welding Smarter, Not Harder: Revolutionizing Strength Testing in the PVF Industry
Strength is paramount in pipes, valves, and fittings (PVF). These components, often carrying vital fluids under immense pressure, rely heavily on the integrity of their welded joints. Ensuring those joints can withstand years of stress is where Stress Concentration Factors (SCF) come in — a critical measurement that’s traditionally been a headache for engineers.
The SCF Bottleneck: A Time-Consuming Necessity
Imagine designing a network of pipes for an oil refinery. Each weld, where pipes of different sizes meet, needs its SCF calculated to ensure it won’t buckle under pressure. The gold standard for this is Finite Element Analysis (FEA) — powerful computer simulations that are incredibly accurate but painfully slow, especially when dealing with hundreds of unique welds.
“It’s like bringing a magnifying glass to every single grain of sand on a beach,” explains Dr. Emily Carter, a leading researcher in sustainable energy and materials science, speaking about the intricacies of material analysis. “[Detailed analysis] gives us a detailed picture of [the subject], but it’s a massive computational undertaking, often creating delays and driving up costs.” [1] While this quote generally refers to material analysis, it aptly illustrates the challenges of detailed FEA simulations in PVF design.
This bottleneck is precisely what researchers Arvind Keprate and Nikhil Donthi tackled in their paper, “Prediction of Stress Correction Factor for Welded Joints Using Response Surface Models.” [2] Their goal? To make SCF prediction faster and more efficient without sacrificing accuracy.

Enter the RSM: A Smarter Way to Predict Strength
Their solution lies in the clever application of Response Surface Models (RSMs). Think of RSMs as intelligent shortcuts — mathematical models trained to recognize patterns and make predictions based on existing data. Instead of running time-consuming FEA simulations for every weld, engineers could use RSMs to get quick, reliable estimates.
To put it simply, imagine an experienced welder looking at a joint and telling you, based on their years of experience, how much stress it can handle. The RSM has ‘learned’ from countless FEA simulations, so it can make informed predictions without rerunning the entire simulation.
Keprate and Donthi put 12 different RSMs to the test, using FEA data as their training ground. They then compared the RSM predictions to actual FEA results, measuring their accuracy using three key metrics:
- RMSE (Root Mean Square Error): How far off the RSM’s predictions were on average.
- AAE (Maximum Absolute Error): The biggest mistake any RSM made, highlighting worst-case scenarios.
- EVS (Explained Variance Score): This score measures how well the RSM captured the overall trends and variations in the FEA data.
Their findings showed that certain RSMs could predict SCFs with impressive accuracy, often within a hair’s breadth of the painstaking FEA results. [2]
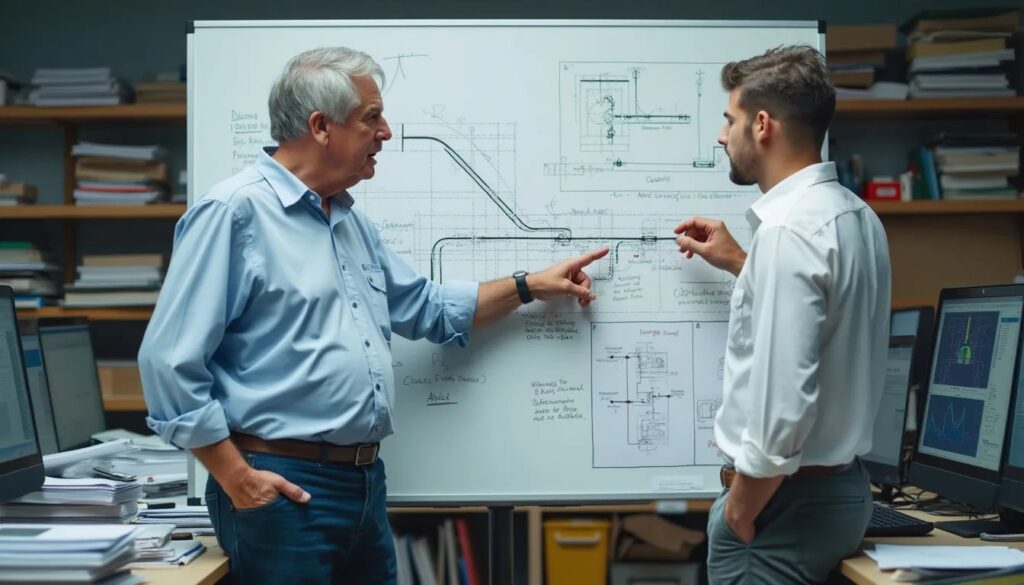
A Seismic Shift in PVF Testing?
While this research is still in its early stages, its implications for the PVF industry are significant. Imagine:
- Faster design cycles: Engineers could rapidly evaluate different design options, optimizing weld placements and geometries for maximum strength without lengthy FEA delays.
- Reduced testing costs: Fewer FEA simulations mean lower computational expenses, freeing up resources for other critical aspects of project development.
- Improved safety margins: More efficient SCF prediction allows for quicker identification of potential weak points, leading to more robust and reliable PVF systems.
However, the widespread adoption of RSMs in PVF testing has its challenges.
- Industry acceptance: Engineers are a conservative bunch, and rightfully so. Convincing them to trust RSM predictions over the gold standard of FEA will require rigorous validation and standardization of these new methods.
- Software integration: For RSMs to become commonplace, they must be seamlessly integrated into the software tools engineers use daily. This requires collaboration between researchers and software developers.
The Future of Strength Testing: A Collaborative Effort
Despite these challenges, the potential of RSMs in PVF testing is undeniable. This research is a prime example of leveraging data and technology to make engineering more innovative and efficient. It’s not about replacing FEA entirely but about using it more strategically and augmenting it with powerful new tools.
The future of PVF strength testing lies in a collaborative approach, where researchers, engineers, and software developers collaborate to refine, validate, and implement these promising new techniques. The result? Safer, more reliable, and cost-effective PVF systems that keep our world running smoothly. •